Platinum resistance sensing elements are generally manufactured in four configurations. Only RdF manufactures all four with the special processes required in each configuration:
Wire-Wound
Film
Coil
Hollow Annulus
The wire-wound, or resistor-style sensing element (see Figure 1), is built by simply winding a small diameter platinum sensing wire around a mandrel constructed of non-electrically conductive material. The winding mandrel has provisions for anchoring a larger lead-wire, which facilitates attachment to external connections. The sensing wire is attached to the larger lead usually by resistance spotwelding and/or high-temperature soldering. The sensing wire is then overcoated with a nonconductive protective coating such as ceramic cement, or glassy coating.
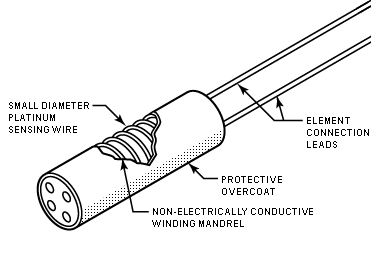 |
Figure 1. The wire-wound sensing element is built by winding a small diameter platinum sensing wire around a nonconducting mandrel |
In the construction of this, or any of the element styles, it is important to match the coefficients of thermal expansion between sensing wire, mandrel, and coating as closely as possible. This minimizes compressive and tensile strain on the small diameter sensing wire. The less strain on the wire, the better the repeatability and stability of the sensor. A good indication of the amount of strain in a sensor is the closeness between the temperature coefficient of the finished sensor and that of the original unsupported sensing wire.
Platinum sensing wire is usually purchased in a hard tempered condition. This makes winding easier, but also requires annealing of the element to obtain the optimum temperature coefficient. This annealing process will also affect the performance of the sensor if it is not done properly.
The second style of sensing element the thin film style is relatively new as a production element, but dominates new general-purpose applications in place of the Figure 1 wound-on-mandrel style. RdF certiified suppliers deposit a thin layer of platinum on a ceramic substrate followed by very high temperature annealing and stabilization. The platinum is deposited in a resistance pattern, usually with provisions for adjusting the final resistance by cutting the circuit in a trim area.
This element is produced in a flat configuration and may be over-molded to other configurations. One advantage of this type of sensing element is that greater resistance can be placed in smaller areas than with other elements. As an example, a 1000Ω sensor is typically manufactured no larger than 1.6mm wide x 2.6 mm long.
 |
Figure 2. The film-type sensing element is made by depositing a thin layer of platinum in a resistance pattern on a ceramic substrate. A layer of glass is applied for protection. |
|
These sensors are typically coated with a thin glassy coating over the resistance grid and with heavy glassy reinforcement over the lead attachment for mechanical and moisture protection. A typical film type sensor is shown in Figure 2. These sensors, being a very thin film, are susceptible to some substrate expansion mismatch and are available with a maximum temperature coefficient of 0.00385ohm/ohm/°C. This solid sensor, combined with RdFs packaging processes, produces extremely rugged RTD assemblies.
The third style sensing element, the coiled element, is manufactured in several different designs, but they all have the same basic goal-to provide a strain-free sensing element. This is done by eliminating the constraints of a normal winding mandrel and overcoating. This freedom minimizes the influence of the mis-match of coefficients of thermal expansion between materials.
 |
Figure 3. The coiled element sensor, made by inserting the helical sensing wires into a packed powder-filled insulating mandrel, provides a strain-free sensing element. |
|
These elements are constructed by starting with a helical coil of platinum sensing wire that resembles a lightbulb filament. The wire is inserted into the internal bores of an insulating mandrel. Powder is packed around the coil to prevent it from shorting and to provide vibration resistance during service. In other versions of this element, the tangent points on the coil are cemented to the winding element or the coil is placed on the outside of a threaded mandrel (or the insulated inner wall of the sensor assembly). Figure 3 shows a typical coiled element manufactured by RdF.
Whatever strain-free method is used, it generally provides a sensor with a higher temperature coefficient and better stability. Of all typical designs, the RdF design, shown here, is the most rugged. All laboratory standard platinum resistance thermometers (SPRTs) are specialized strain-free designs.
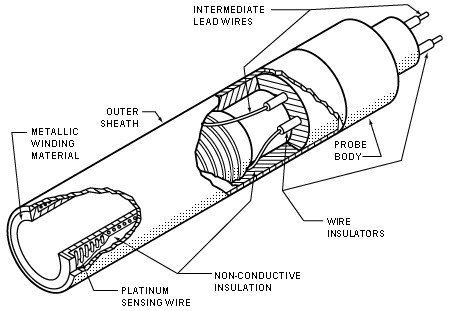 |
Figure 4. The hollow annulus-type element is made by winding platinum sensing wire around a hollow corrosion-resistant metal mandrel. The entire unit is coated with an inuslating material. |
|
The last style, the hollow annulus sensing element, uses an open-ended metal winding mandrel which increases fluid contact and lowers thermal mass to provide a faster time response. In a typical design, shown in Figure 4, the winding mandrel fabricated from weldable corrosion resistant metal is machined to eliminate the internal mass. The winding area is coated with an insulating material and the sensing wire-wound to a predetermined value. The element is then covered with a coating of insulating material. This sensor has a thin external metal sheath welded over the winding area when it is used with no additional housing.
This element has the advantages of being completely sealed and having an extremely fast time response, but it is the most expensive of the four types. The large winding diameter enables high resistance sensors to perform optimally in cryogenic fluid applications.
Each of the four sensing elements discussed has advantages and disadvantages. Before purchasing an RTD assembly, it is advisable to know what type of element the manufacturer is intending to provide and its limitations.
|