RdF Heat Flux Sensors, for the precise measurement of heat loss or gain through materials.
To simplify the measurement of thermal transfer or movement, RdF Corporation has developed a unique line of Heat Flux Sensors to meet a broad range of measurement applications. Specifically, the RdF Heat Flux sensor is designed to obtain a precise direct reading of thermal transfer through a surface in terms of energy per unit time, per unit area.
Standard and custom RdF Heat Flux Sensors are used in virtually every economic activity and a myriad of research and development programs.
HEAT FLUX VS. SURFACE TEMPERATURE MEASUREMENT
The techniques of surface temperature measurement and their instruments are well known. Surface temperature measurements are perfectly satisfactory for applications in which only the immediate, single surface temperature data is required. However, the temperature of a single or outer surface is typically the result of a thermal condition acting upon an inner surface as well as the thermal properties of the total material thickness.
Heat flux sensing devices are the only practical way of accurately measuring the thermal activity at one material surface resulting from thermal events at both sides of that material. A change in heat transfer is also a large directional signal preceding significant temperature change, providing a new tool for critical process control.
EASY TO USE
Applications for RdF Micro-Foil® Heat Flux Sensors are practically unlimited, due to their high performance and reliability, and ease of installation.
The sensors are very thin and flexible and attach to flat or curved surfaces without damaging those surfaces. They require no special wiring, reference junction or signal conditioning. One obtains a heat flux measurement by mounting the sensor and connecting it to any direct-reading microvolt meter or data system. Upon connecting the leads, the sensor provides a direct measurement of the heating or cooling transfer rate through both the sensor and its mounting surface in BTU's or other units. There is a direct relationship, the RdF supplied calibration factor, between the output and the heat flux rate.
HOW MICRO-FOIL® HEAT FLUX SENSORS WORK
A Simplified Explanation1
The function of a heat flux sensor is to measure heat transfer (loss or gain) through the surface where it is mounted. It does this by indicating temperature difference between opposite sides of a thin layer of separator material to obtain a direct measurement of the heat loss or gain through the separator material. The same measured heat must flow through the sensor cover layers on each side of the separator material and the surface where the sensor assembly is mounted.
Before heat flux sensors were developed, the typical method for determining heat gain/loss transfer was to install two temperature-measuring devices, one on either side of the subject material. (See Figure A). The difference between the two temperature readings was then used to calculate heat loss or gain per unit area and unit time through the surface provided the thermal characteristics of the subject material were known. 
In most situations it is neither desirable nor possible to install temperature-measuring devices on both sides of a rigid material — even if thermal characteristics of the material are known. The heat flux sensor reports these same heat transfer measurements from a single, convenient surface with instantaneous readout. In addition, precise properties of the surface material are not required.
In our simplified explanation, heat flux sensor (see Figure B) construction is much like the example shown in Figure A. Two temperature–measuring thermocouple elements are physically separated by a thermal insulating material, but now oriented and connected to oppose each other. Combined output is zero when there is no temperature difference. When the heat begins to “transfer” through surface and increase (T1), junction (J1) generates an increased voltage. As the heat passes through the material (I1) to reach thermocouple junction (J2), the voltage at (J1) is always higher to generate a differential voltage output. As the temperature of J1 is warmer (or cooler if heat is coming from the other direction) than the temperature of J2 , that temperature differential, creates a similar and directional differential in voltage. Since the temperature differential is proportional to heat flow/unit area and unit time, so is the voltage differential output, with its polarity indicating the direction of the heat flow.
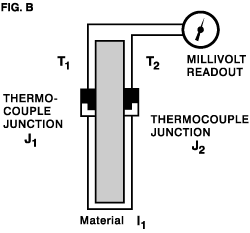
If such a heat flux device were to be embedded within a subject material, it would tend to become an integral part of that material—duplicating and reading out the heat transfer/unit area and unit time through the composite material and sensor.
Due to the unique design of the RdF Micro-Foil® Heat Flux Sensors it is not necessary to implant or in any way damage or invade the subject surface in order to achieve highly reliable and precise readings. (See Figure C). The RdF Heat Flux Sensors are extremely thin and flexible so that when properly mounted they become virtually a “component” of the subject surface. The RdF Heat Flux Sensor faithfully simulates the action and reaction of the temperature changes (transfer of heat) at the sensor mounting surface because the same heat must flow though one, then the other.

UNIQUE CONSTRUCTION
Conventional heat flux sensors fabricated with wire tend to create excessive thermal losses at the edges of the sensor because they are at least 10 times thicker than RdF sensors. Most are also rigid, applicable only on flat surfaces.
RdF’s patented Micro-Foil® Heat Flux Sensors are fabricated with special homogeneous alloys and extremely thin foil legs between junctions. This enables thin and flexible construction. Equally important, RdF forms the sensor junctions in high heat flux sensors by a unique process that joins dissimilar metal foils without any overlap so ideal heat flow is not diverted. The complete fabrication process produces in a very thin, strong, and flexible sensor unit.
CALIBRATION
RdF Micro-Foil® Heat Flux Sensors are individually calibrated at a base temperature of 70°F (21°C). Generally, the sensor is calibrated for low levels by conduction in heat flow series with a traceable standard. The result is a calibration constant for microvolt output per unit of heat transfer rate. Models with heat sinks for high heat flux are calibrated for millivolt output at traceable levels of thermal radiation over the range and a curve is supplied. Calibration curves are typically linear. Each sensor is individually packaged with its calibration data.
1 See Application note PA-HFS, “Simplified Heat Flow Measurement”, for technical specifics. The purpose of this text is to convey by general analogies a basic understanding of heat flux sensors and their potential applications.
|